Proprietà della nichelatura chimica
Durezza e Resistenza all'usura
Durezza
I rivestimenti NIPLATE® possiedono una durezza notevolmente superiore rispetto a quella dei substrati tipicamente ricoperti, e questo contribuisce ad accrescere le loro proprietà tribologiche. In confronto ai rivestimenti tradizionali e commercialmente comparabili (come il nichel elettrolitico, ossidazione anodica dell'allumino, e trattamenti termochimici degli acciai), essi manifestano una durezza mediamente più alta, paragonabile a quella del rivestimento di cromo duro.
Tuttavia, è da notare che la durezza del nichel chimico è inferiore rispetto ai rivestimenti speciali, quali plasma spray, PVD/CVD, i quali, però, presentano notevoli differenze in termini di costo e di applicazione.
Nella tabella sottostante, sono sintetizzate le durezze dei rivestimenti che possono essere ottenute in relazione ai trattamenti termici eseguiti:
Durezza [HV] | Deidrogenazione 150-180° C x 4h | Indurimento 260-280° C x 8h | Indurimento 330-350° C x 4h |
---|---|---|---|
NIPLATE® 500 | 550 ± 50 HV | - | 1000 ± 50 HV |
NIPLATE® 600 | 700 ± 50 HV | 800 ± 50 HV | 1000 ± 50 HV |
NIPLATE® 500 PTFE | 250 ± 100 HV | 300 ± 100 HV | - |
NIPLATE® 600 SiC | 700 ± 50 HV | 850 ± 50 HV | 1050 ± 50 HV |
CONSIGLI PRATICI
La massima durezza dei rivestimenti NIPLATE® si può ottenere attraverso un trattamento di indurimento a 340° C per 4 ore. Questo processo provoca una colorazione giallo-blu iridescente del rivestimento. Se necessario, è possibile effettuare un trattamento termico di indurimento in atmosfera inerte. Questo metodo permette di raggiungere la massima durezza del rivestimento, mantenendo inalterata la colorazione bianca metallica del nichel chimico.
Resistenza all'usura
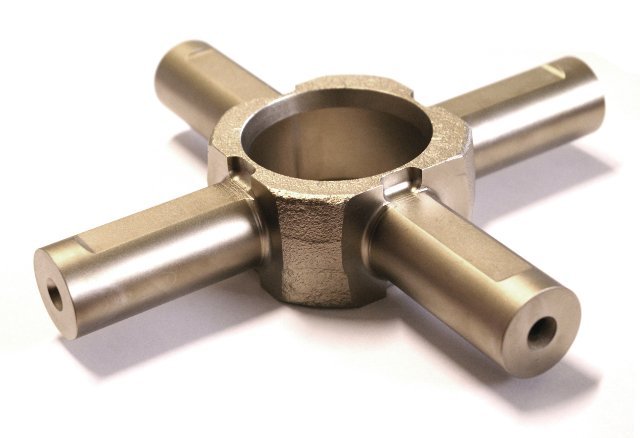
Grazie alla loro durezza e coesione, i rivestimenti NIPLATE®, in particolare il NIPLATE® 600 ed il NIPLATE® 600 SiC, permettono di ottenere una elevata resistenza all'usura delle superfici trattate.
Il NIPLATE® 600, con un contenuto del 7% di fosforo in lega, offre un'alta resistenza all'usura abrasiva, all'usura adesiva e al fretting, sia in ambiente lubrificato che a secco. La durezza raggiunta con i trattamenti termici di indurimento e gli alti spessori di rivestimento ottenibili (fino a 50-70 µm) permettono di incrementare la vita del componente e ottenere una resistenza all'usura simile al cromo duro, con il vantaggio di non dover rettificare successivamente il pezzo e di avere uno spessore di rivestimento uniforme su tutta la superficie, sia interna che esterna.
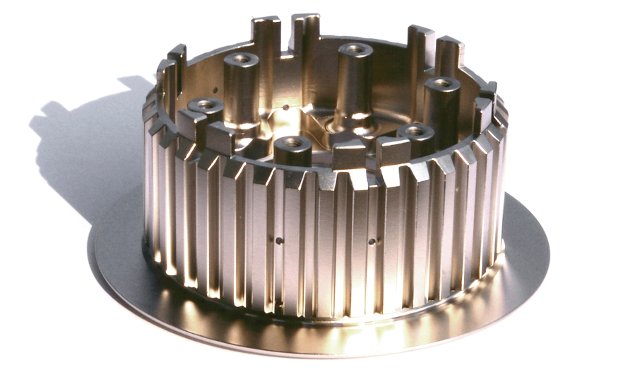
Per applicazioni critiche, dove l'usura del componente è massima, è stato studiato il NIPLATE® 600 SiC, rivestimento composito a matrice NIPLATE® 600 contenente grani micro-cristallini di carburo di silicio in quantità del 20-30% in volume. Le particelle di carburo di silicio, materiale ceramico sintetico ultra-duro, permettono di ottenere un rivestimento con caratteristiche di resistenza all'usura straordinarie. La resistenza all'usura abrasiva del NIPLATE® 600 SiC è fino a 10 volte maggiore di quella del cromo duro. Questo rivestimento viene utilizzato in settori altamente tecnologici, ad esempio nel racing per incrementare le prestazioni senza diminuire la vita dei componenti, o nel tessile per proteggere i componenti soggetti all'usura costante del filo di tessitura.
CONSIGLI PRATICI
- Per componenti soggetti a forte usura, prevedere uno spessore di trattamento di almeno 20 µm e un successivo trattamento di indurimento a 280° C per 8 ore o meglio ancora a 340° C per 4 ore.
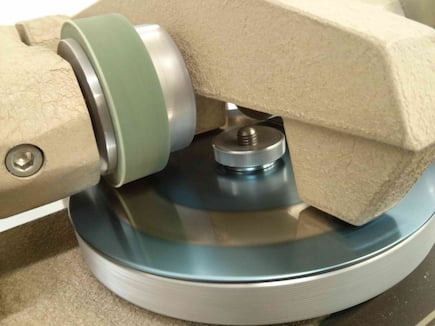
Test di usura abrasiva Taber Abraser
Il test più utilizzato per la misura della resistenza ad usura abrasiva sui rivestimenti è il Taber Abraser Test. La prova di usura sui rivestimenti di nichel chimico è specificata dalla normativa americana ASTM B733. I parametri di prova sono i seguenti:
- Ruote abrasive: CS-10
- Carico su singola ruota: 1000 g
- Altezza ugelli aspirazione: 1 mm
La prova viene effettuata montando i provini su un piatto rotante, sottoponendoli al contatto di due ruote abrasive che rotolano e contemporaneamente strisciano, sotto l'applicazione di una forza specifica. I residui di usura durante la prova sono aspirati per mezzo di due ugelli posizionati sopra il provino. Al termine della prova di usura viene calcolato il Taber Wear Index (TWI), indice dell'usura subita dal rivestimento, calcolato come variazione media di peso espressa in mg su 1000 cicli.
Nella seguente tabella sono riportati i valori di TWI dei rivestimenti NIPLATE®. Un basso valore indica una resistenza all'usura abrasiva maggiore.
Resistenza all'usura [TWI] | Deidrogenazione - 150-180° C x 4h | Indurimento - 260-280° C x 8h | Indurimento - 330-350° C x 4h |
---|---|---|---|
NIPLATE® 500 | 20 TWI | - | 10 TWI |
NIPLATE® 600 | 16 TWI | 12 TWI | 9 TWI |
NIPLATE® 500 PTFE | 33 TWI | 19 TWI | - |
NIPLATE® 600 SiC | 0,70 TWI | 0,65 TWI | 0,60 TWI |